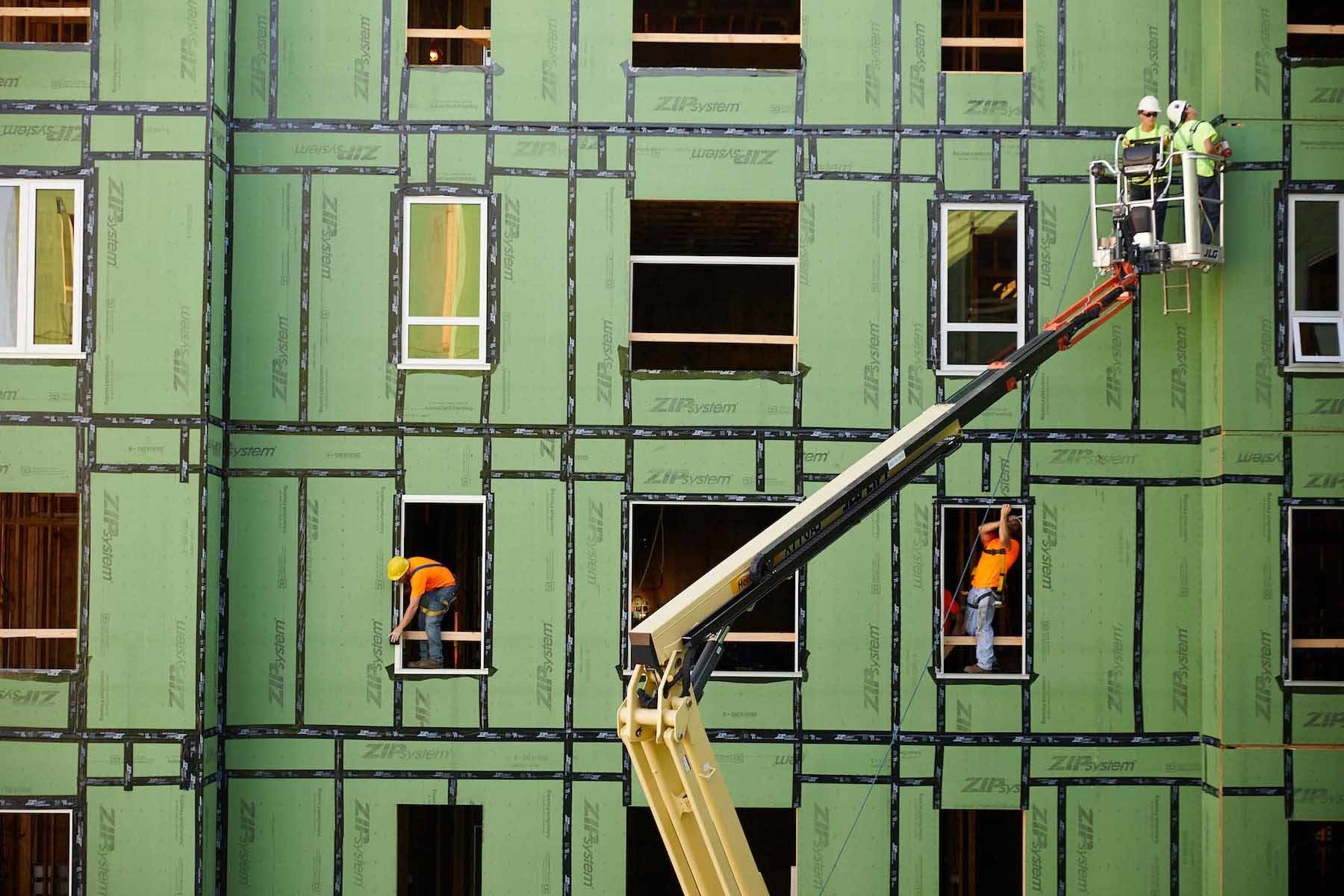
Detailing Barrier Continuity in Building Enclosures
4 Min Read April 10, 2018
The role of the building enclosure is to provide protection for the exterior and interior of the structure. Separation is accomplished using four primary types of barriers: water-resistive barriers (WRBs), air barriers, thermal barriers and vapor retarders. All of them are intended to restrict or control the passage of a targeted item (water, air, heat or moisture) through a roof, wall or foundation system.
While this can seem straightforward along flat, continuous surfaces, it is the non-continuous conditions that present design and construction issues. These can include transitions from one material to another, penetrations, interruptions caused by planned openings such as windows and doors, or changes in surfaces such as roof/wall junctions or parapets.
The key to continuity in building enclosure systems is a careful and coordinated approach to consistent detailing. Understanding the choices and developing complete details as part of construction drawings is the best way to ensure continuity in the building’s enclosure for an airtight, weather-resistant exterior that promotes energy efficiency and long-term durability.
Choices in barrier systems
As with most design and construction systems, there are options available for how to achieve each of the four barriers and their continuity on, and around, a structural framing system.
The conventional approach is to use a multiproduct, multilayer design in which each of the four barriers is specified and installed as a separate layer in an assembly. This requires specifying multiple products that need to be compatible. Each serves a single function and has individual installation requirements, often performed by different trades during construction, which can raise the risk of delay or incorrect installation, increasing the need for coordination. Further, to be sure that their installed performance will be satisfactory, the particular combination of products needs to have been tested to ensure they meet all of the water, air and thermal thresholds required for the assembly. There also needs to be proper detailing between the materials to ensure the total system will work as intended.
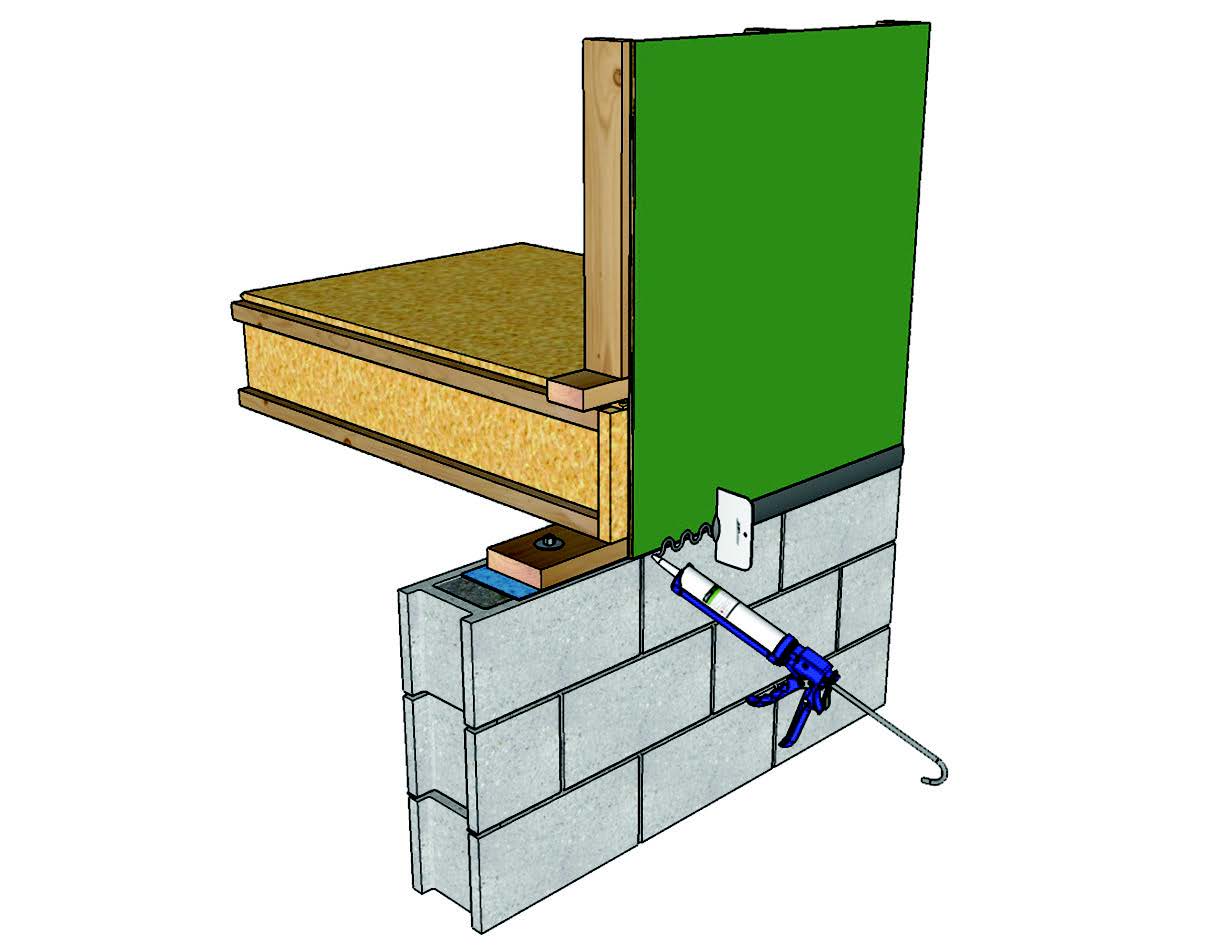
As an alternative, there are integrated sheathing product solutions that have become available. One of the most common transitions design and build teams make is replacing the sheathing-plus-housewrap assembly with ZIP System® sheathing and tape, eliminating the need for housewrap. The newest addition to the ZIP System brand of products is ZIP System® R-sheathing, which additionally incorporates built-in polyisocyanurate foam exterior insulation.
A revolutionary approach to building enclosures, ZIP System sheathing and tape products streamline the weatherization process with an integrated air and water-resistive barrier and advanced-acrylic tape for panel seams and flashing details that deliver moisture and air protection in one easy-to-install system.
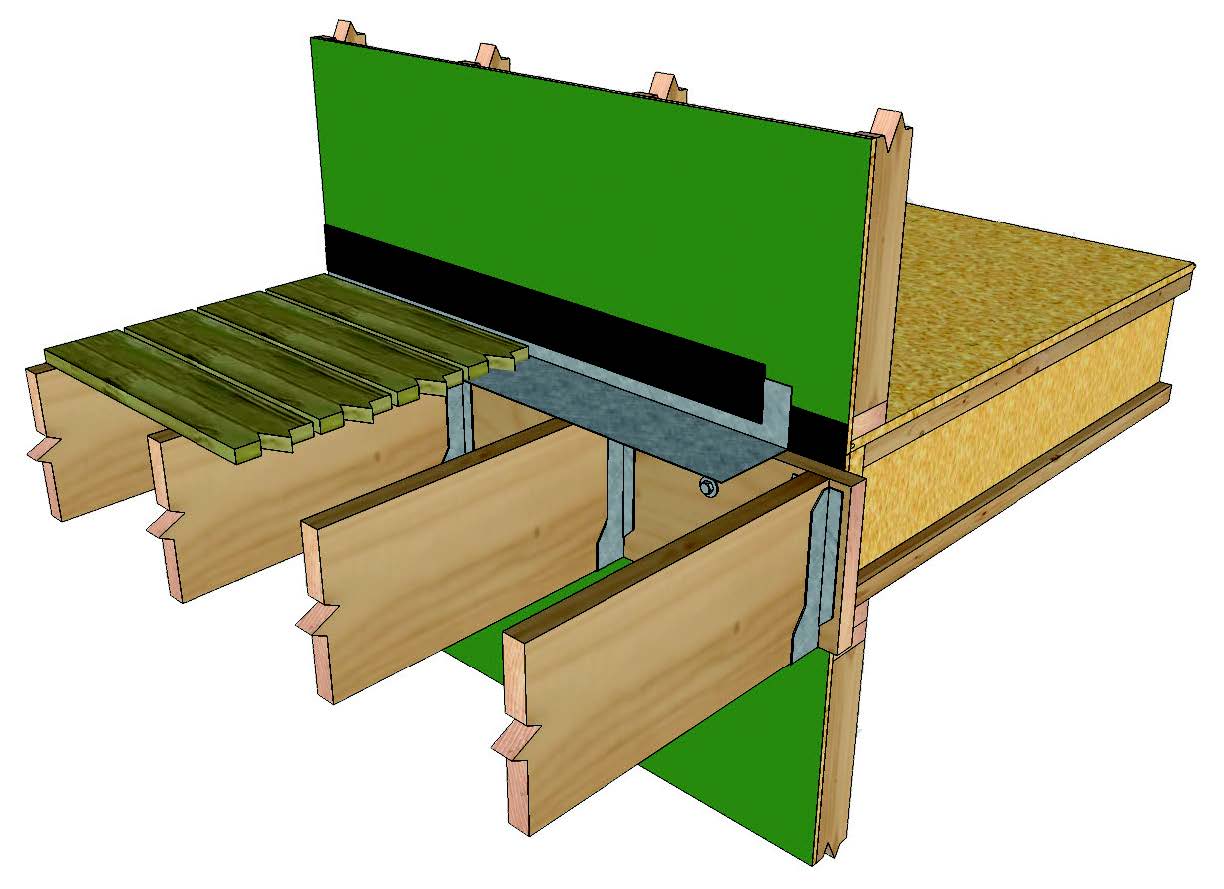
This means that a single, high-performing engineered wood sheathing product can be specified, used as the basis of design and installed by a single trade to achieve water, air and thermal barriers. This online course will show detailed specifications for critical transitions in places like windows, doors and wood to masonry when specifying wall assemblies using ZIP System sheathing and tape with an integrated water-resistive barrier onto the surface of the engineered wood sheathing.
The 2015 IECC now includes prescriptive requirements for exterior continuous insulation in certain climate zones. ZIP System R-sheathing includes a thermal barrier of continuous insulation in a variety of thicknesses to help achieve the right R-value for your wall design. Installed with the exterior wood panel with the integrated water-resistive barrier on the outside, it creates a solid, nailable, easy-to-flash base for exterior cladding systems and transitional areas. The pre-applied continuous foam insulation is on the back of the sheathing and is installed against studs using manufacturer-prescribed fastening schedule and screws to achieve necessary shear strength. To ensure the best continuity of air, water and thermal barriers with ZIP System sheathing products, this course reviews how to detail areas such as joints, penetrations and openings using ZIP System™ flashing tape, ZIP System™ stretch tape and ZIP System™ liquid flash.
The full CEU course will explain in-depth the continuity issues of the four primary barriers and review a series of drawings and details that can help accomplish a continuous building enclosure system on critical transitions. Learn more about ZIP System sheathing and tape by visiting ZIPRevolution.com.
Contact your Huber representative or email aiaceu@huber.com to schedule and in-person training session.