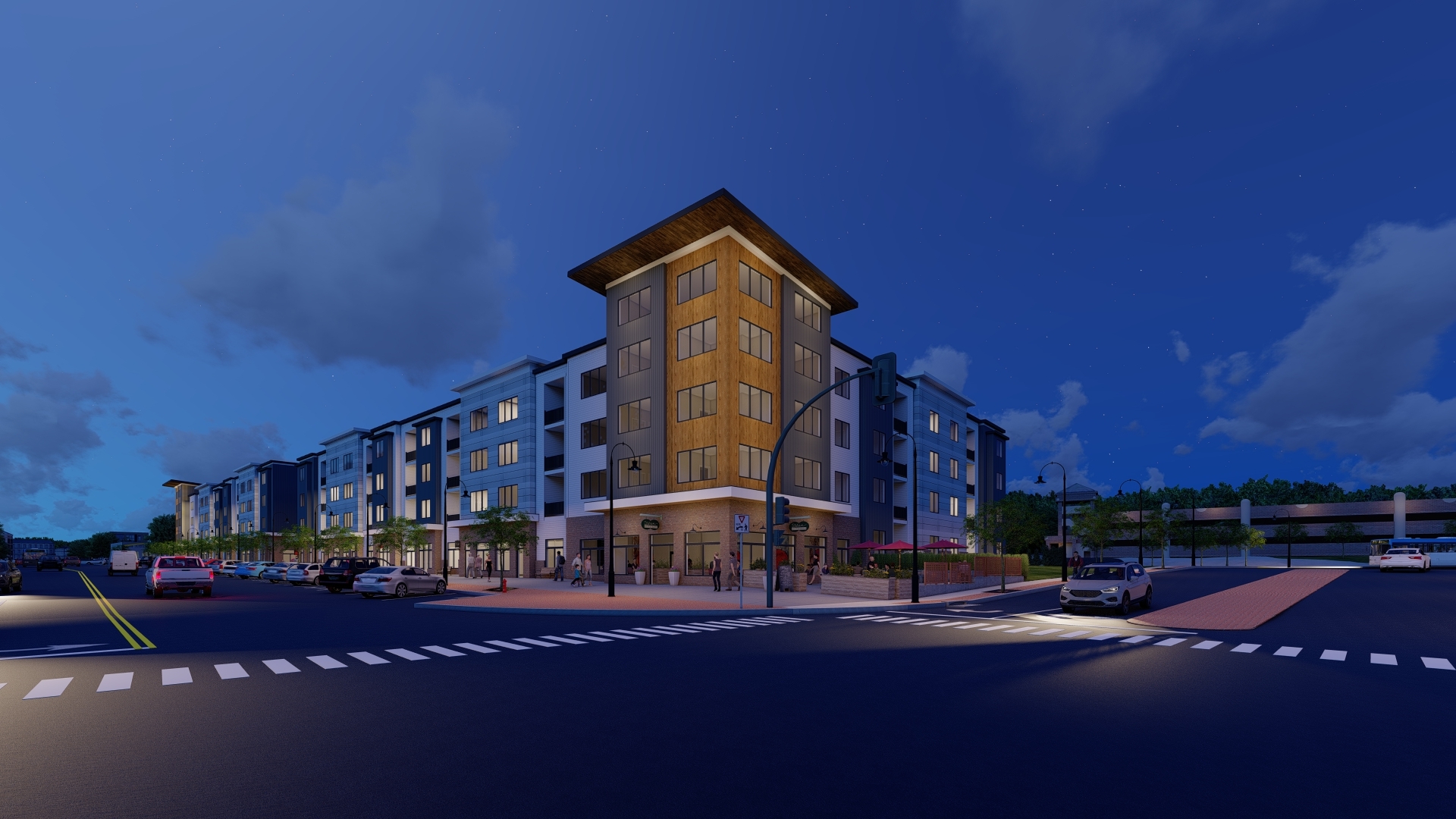
Faster, Drier, Smarter: A Multifamily Builder’s Switch from Gypsum Concrete to EXACOR® Underlayment
7 Min Read November 8, 2024
In Bristol, Connecticut, By Carrier opts for EXACOR® underlayment, prioritizing efficiency and durability for a 104-unit apartment development project.
When Ryan Carrier, owner and construction manager of By Carrier, embarked on a mixed-use apartment development project in downtown Bristol, Connecticut, he recognized the importance of meticulous material selection to bring his vision to life. Spanning two four-story buildings housing 104 apartments, the Centre Square Village project demanded labor efficiency and impeccable craftsmanship. Having relied on gypsum concrete in previous projects, Carrier recognized its logistic hurdles and prolonged drying periods as potential setbacks.
Seeking a more efficient and reliable alternative, Carrier turned to EXACOR® underlayment panels, known for their durability and streamlined installation process. The choice ensured smooth progress throughout the construction of Centre Square Village, a future luxury apartment community in the city’s bustling North Main Street district.
“Centre Square Village is the first project we have used EXACOR products on,” Carrier said, “but we’ve used other Huber Engineered Woods products, including AdvanTech products, for many years. We committed to using EXACOR® underlayment material during the pre-construction/drawing phase, deciding on that very early.”
The Centre Square Village project, which started in July 2023 and is scheduled for completion in 2025, includes 15,600 square feet of commercial space, the majority of which will be used for restaurants with outdoor dining space. Incorporating EXACOR underlayment panels throughout the construction process contributed to significant time savings, with Carrier estimating a reduction in the build timeline by around three weeks per building. Read on to see how.
5 Key Advantages that Drove the Switch to EXACOR Underlayment
EXACOR underlayment panels offered several advantages over traditional gypsum concrete, particularly in efficiency and ease of installation.
“With gypsum, logistically, it’s a little bit more complicated because you can’t have anybody else working inside at the same time,” Carrier said, “so you’re losing some really valuable time.”
Take a closer look at the advantages that drove Carrier to make the switch.
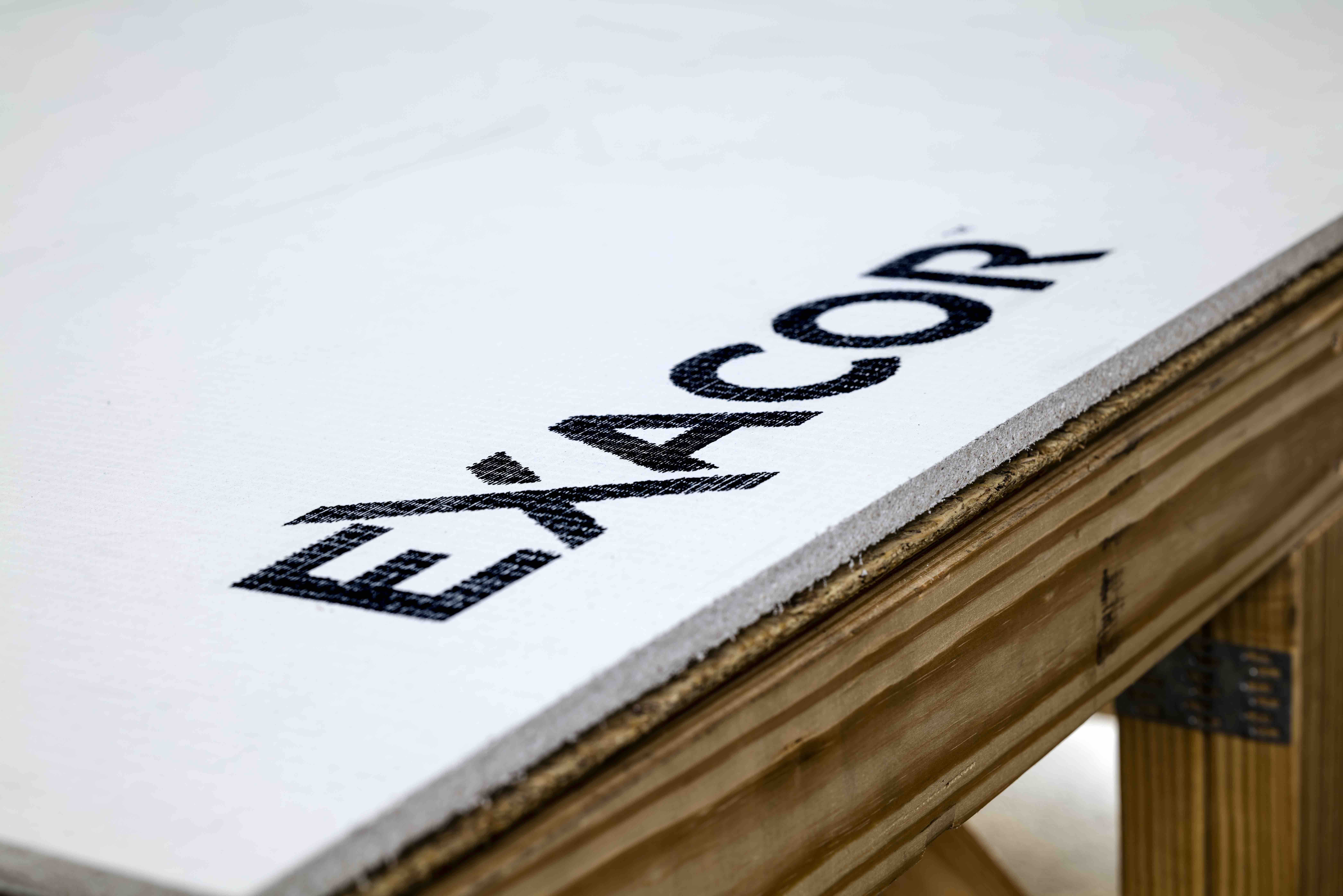
1. EXACOR Underlayment Can Be Installed by Framers
Carrier was initially intrigued by the prospect of using EXACOR underlayment panels due to the simple installation process, which can be handled by the framing crew itself. This eliminated the necessity for specialized teams required for gypsum concrete, marking a significant shift in efficiency and cost-effectiveness.
“We have always used gypsum, so when I heard about this product, it sounded too good to be true,” Carrier said. “I was like, ‘Wow — the framers can install this stuff? This is amazing.’”
Unlike gypsum concrete, which typically requires dedicated crews and extended drying times, EXACOR underlayment is designed for easier handling and quicker installation. The panels can be cut and installed with standard tools, reducing the need for specialized equipment or skills.
“Even our subcontractors recognized the efficiency gains,” he said. “Once they understood the right techniques, they were able to work more effectively.”
This adaptability and ease of use not only streamlined the installation process but also minimized training requirements for the crew, allowing them to efficiently integrate EXACOR underlayment into the construction workflow of Centre Square Village.
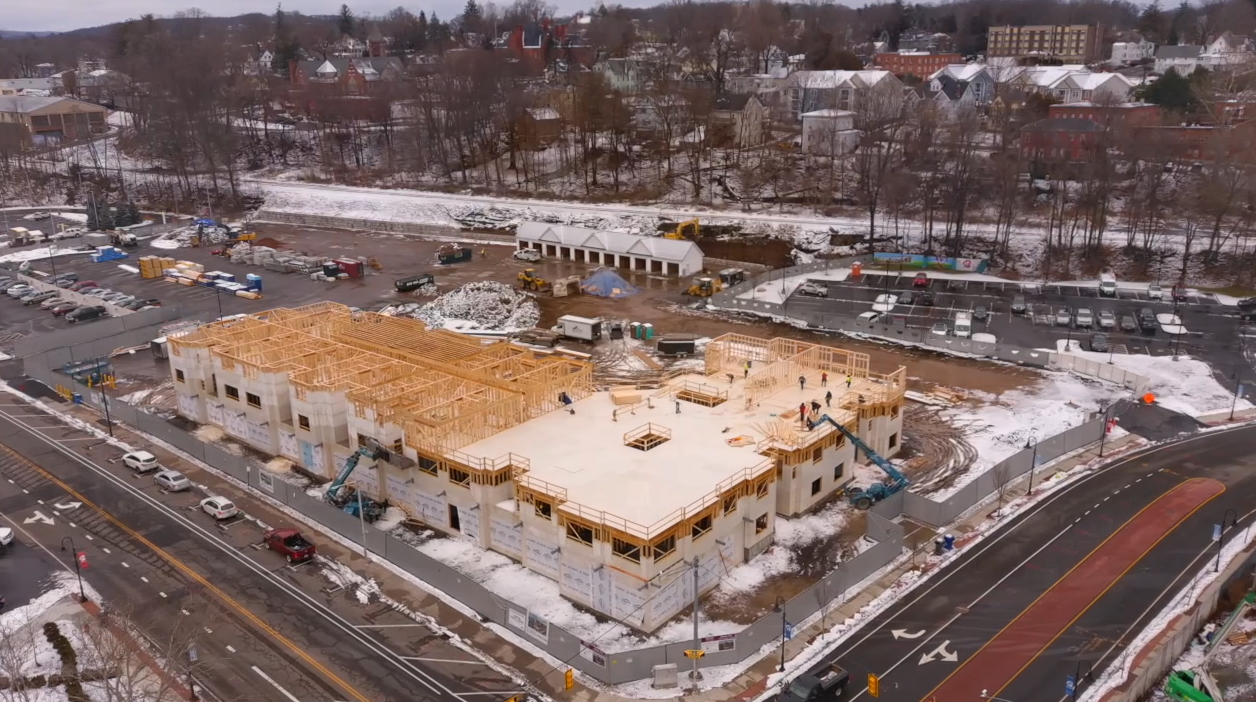
2. Three to Four Weeks of Time Saved
The adoption of EXACOR underlayment panels rather than gypsum concrete has revolutionized the efficiency of construction at Centre Square Village. Unlike traditional methods that require extensive curing time, specialized materials and dedicated crews, EXACOR panels streamline cycle times by eliminating these dependencies on water-based gypsum underlayment installations. This not only accelerates project timelines significantly but also upholds critical attributes such as sound and fire protection, which are essential for high-quality residential developments.
We easily gained three to four weeks in our schedule because we decided to use EXACOR panels over gypsum, between cleaning up to prepare for the gypsum trucks and installation and drying time. –Ryan Carrier, owner and construction manager for By Carrier
“I had high hopes for the product and it delivered,” Carrier said. “We easily gained three to four weeks in our schedule because we decided to use EXACOR panels over gypsum, between cleaning up to prepare for the gypsum trucks and installation and drying time.”
The numbers don’t lie: According to third-party testing by Home Innovation Research Labs, EXACOR panels were found to install 30% faster than traditional wet-laid gypsum in flooring underlayment applications on wood-framed flooring systems typical of multifamily builds.
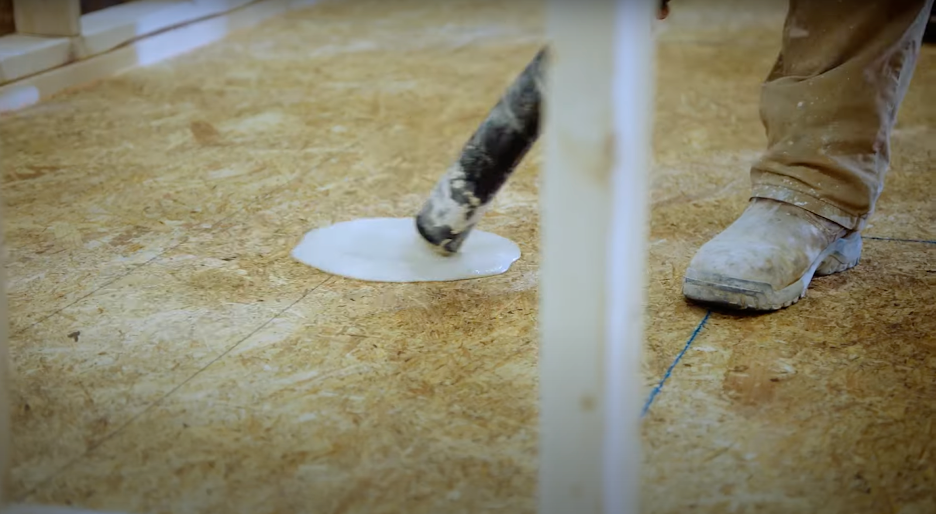
“The product costs a little more initially, but the time and labor saved using MgO panels versus gypsum makes it a clear choice,” Carrier said. “Just knowing that the framers can put down this 1/2" product right on top of their 3/4" subfloor before the walls went up — it almost doesn’t impact your schedule at all.”
3. Superior Moisture Control
Beyond expediting construction timelines, MgO panels such as EXACOR panels offer unexpected advantages by not introducing moisture into the building, crucially impacting project efficiency. Unlike gypsum concrete, which is required to be mixed with water for installation, EXACOR is installed as a dry panel solution. In wood-framed construction, this reduces the risk of elevated humidity levels and moisture-related issues during and after installation, which can often necessitate time-consuming ventilation management.
“One of the standout advantages we observed is the superior moisture control compared to traditional gypsum,” Carrier said. “With gypsum, moisture levels inside the building can spike and remain elevated for several days, posing risks for mold and necessitating extensive ventilation measures.”
EXACOR panels effectively reduce the amount of moisture added to the building. Their inherent moisture resistance and quick installation process reduce the need for prolonged ventilation and enhance operational efficiency by minimizing the risk of moisture-related delays.
4. Adhesion to Flooring
Carrier had initial concerns about how well EXACOR panels would adhere to flooring. However, he was quickly reassured by the Huber Engineered Woods technical teams, who provided a comprehensive compatibility chart specifying all the approved adhesives suitable for LVPs and tiles. The resource ensures that installers can confidently select adhesives that will securely bond with EXACOR underlayment panels, facilitating smooth and reliable flooring installations. Huber Engineered Woods collaborated closely with adhesive manufacturers to rigorously test and evaluate compatibility.
“The only hesitation that I would say I had was adhesion for flooring,” Carrier said, “but the HEW team put that to rest pretty quickly.”
5. Ease of Adoption for Builders
The uptake of EXACOR underlayment panels among building professionals like Carrier isn’t just about keeping up with modern construction practices — it’s about diving headfirst into new technology that amps up efficiency, cuts costs and keeps quality top-notch.
“A lot of builders are old-timers, and they’re not very quick to make changes — they’ve had a product that they’ve worked with for their whole life and they’re comfortable with it,” Carrier said. “Being a little bit younger and coming across a lot of new products, I wanted to give EXACOR panels a shot.”
Moreover, the swift acceptance of MgO underlayment panels establishes a practical precedent for future advancements in construction materials and techniques. Builders who embrace these innovations early gain a competitive edge by delivering projects more efficiently and with improved durability, giving them a leg up in the competitive game of building better.
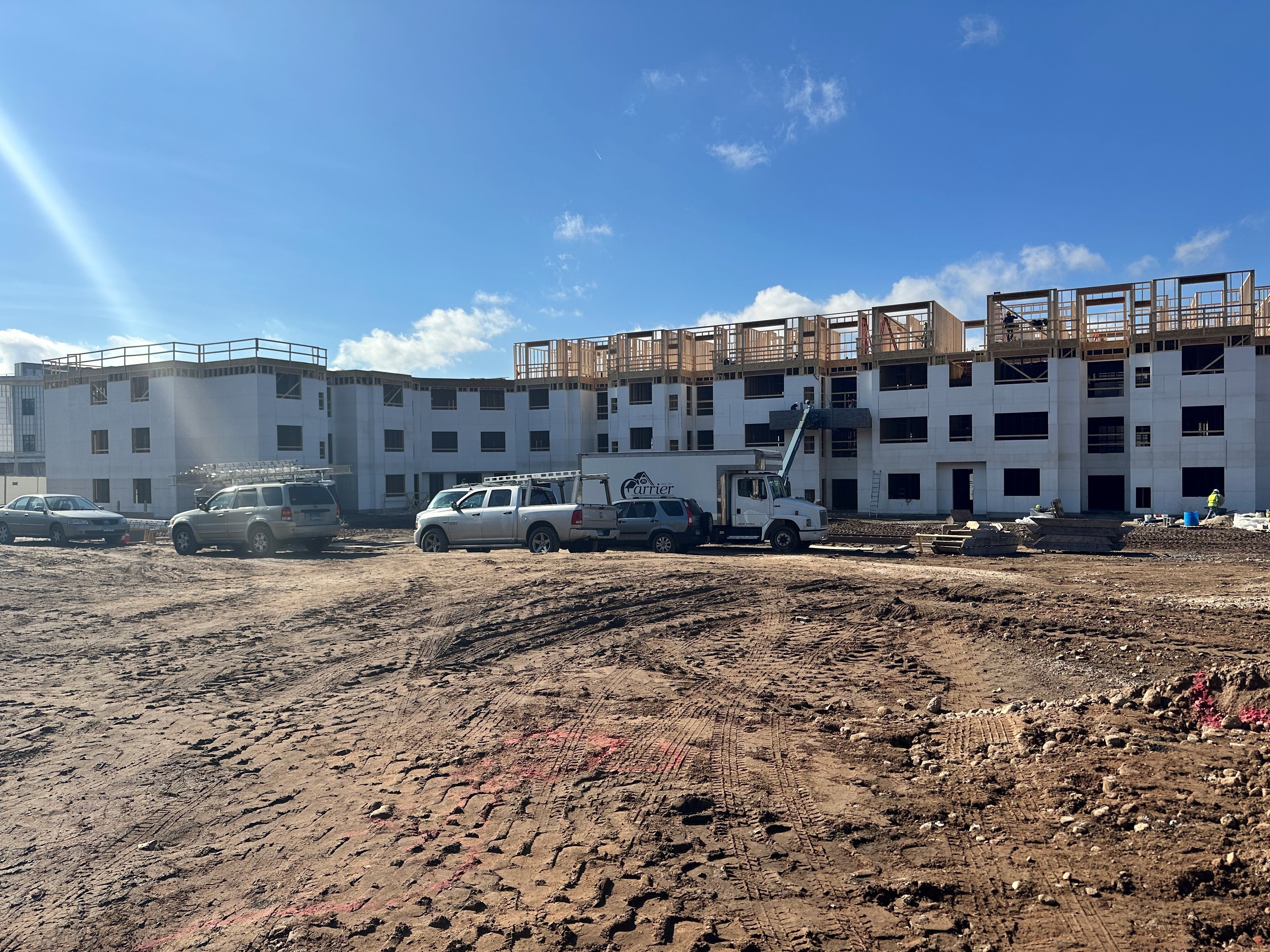
The Future of Flooring Systems with EXACOR Underlayment
Throughout the construction of Centre Square Village, the benefits of EXACOR underlayment panels became unmistakably clear. Offering enhanced durability, quicker installation times, superior moisture control and a reduced environmental impact, the panels not only streamlined project timelines but also upheld stringent standards of structural integrity.
As builders increasingly prioritize efficiency and sustainability, the widespread adoption of EXACOR underlayment panels establishes a promising model for future innovations in construction technologies. By embracing these advancements early on, builders can significantly improve project outcomes and maintain a competitive edge in the evolving construction industry.
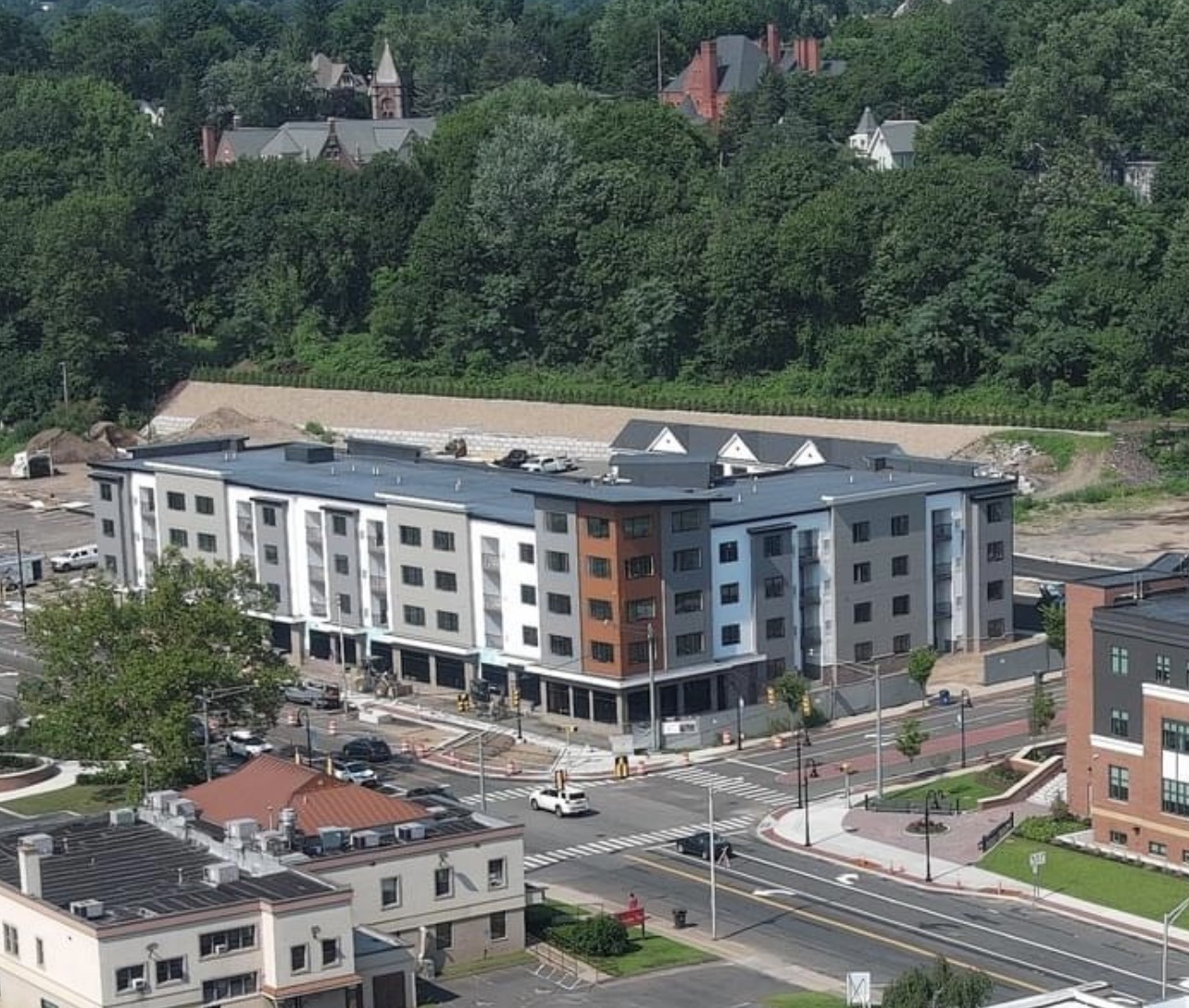
“Huber Engineered Woods is a very well-known and reputable company,” Carrier said, “so if they’re making a product, it’s going to be a good one.”