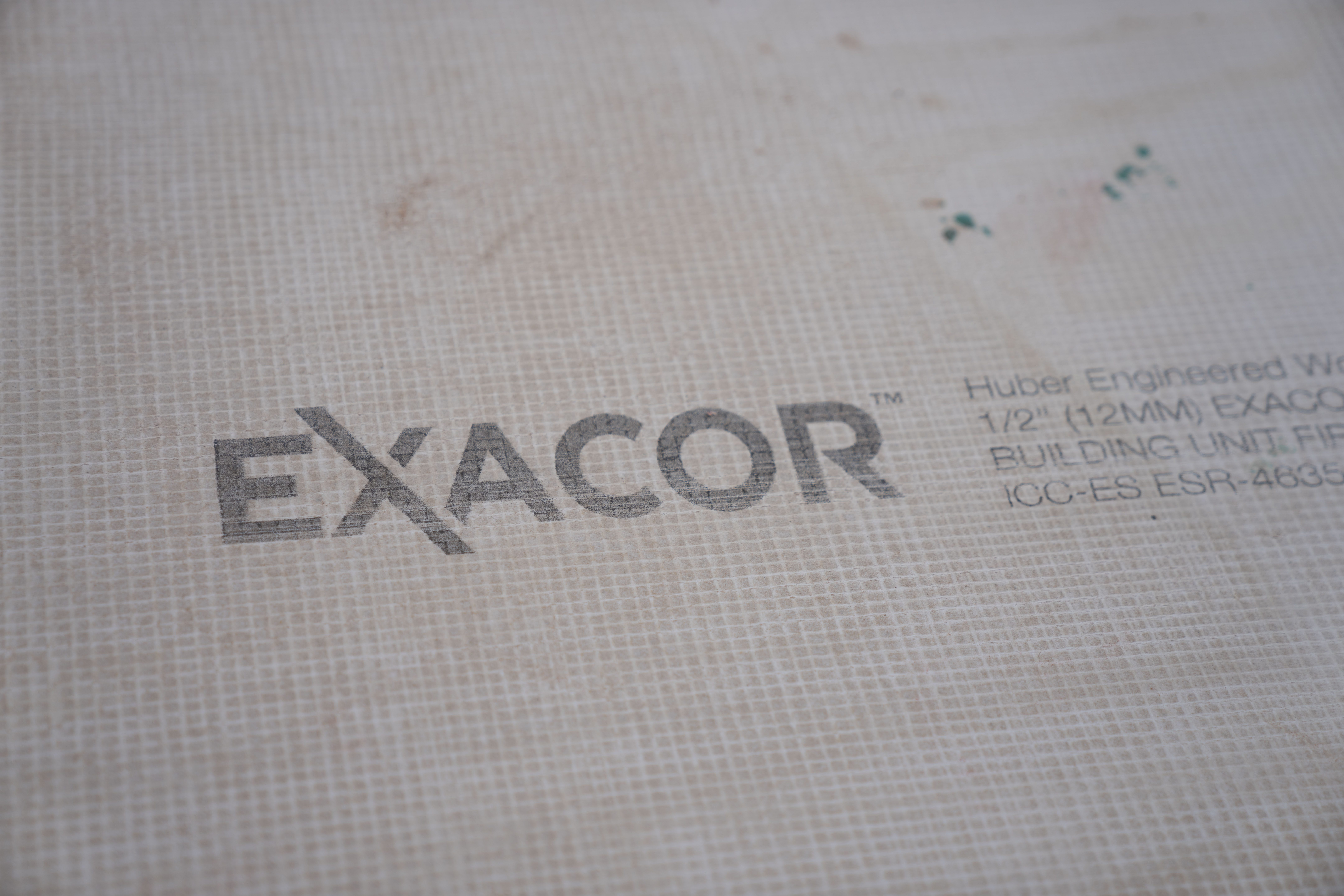
Game-changer: The Impact of EXACOR® Underlayment Panels
3 Min Read May 9, 2024
Exploring EXACOR® Products: A Modern Construction Solution
In today's ever-evolving construction scene, it's all about keeping up with new innovative technologies with new construction materials. Teams are diving into fresh technologies like EXACOR® floor underlayment panels to easily tackle client demands. No more grappling with the hassles of wet-laid gypsum EXACOR has got your back.
EXACOR panels are turning the traditional use of wet-laid gypsum on its head, especially in multi-family and commercial construction. They bring solid sound and fire protection to OSB or plywood floors, with fewer materials and faster installation times. These ½” underlayment panels are crafted from magnesium oxide (MgO) with a sturdy mesh core, ensuring stability and a snug fit.
See the difference between EXACOR panels and traditional wet-laid gypsum.
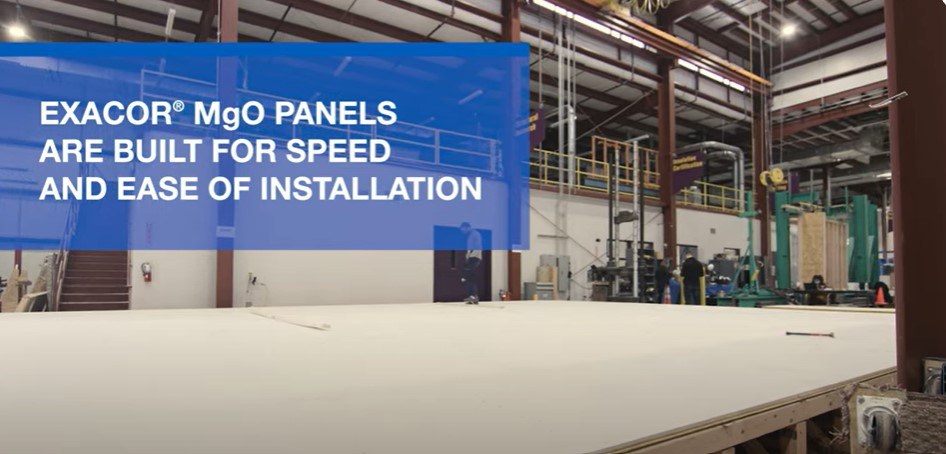
Meeting Code Requirements with EXACOR® Panels
When it comes to meeting or even surpassing STC/IIC rating code requirements, assemblies utilizing EXACOR underlayment panels are top-notch. They've been put through the paces and tested according to Section 1206 of the 2021 International Building Code. Say goodbye to specialty crews and the headache of water-based processes—EXACOR is versatile enough for many residential, light commercial, and multi-family construction projects.
Take a look at our technical library for more details on EXACOR’s fire and sound rated assemblies.
Ridgehouse Construction's Experience with EXACOR® Underlayment
Take it from Ridgehouse Construction's experience in Arizona—EXACOR is a game-changer. Matt Limpert, Regional Vice President, couldn't sing its praises enough for long-term cost savings and time savings.
“We tried out EXACOR on a project in Alabama before, and after using the ½-inch panels instead of ¾” gypcrete we saw the time and cost savings firsthand,” Limpert shared. “We ran our own tests on sound and density, and it was a no-brainer to switch to EXACOR for our Arizona projects.”
Ridgehouse Construction’s track record of multifamily projects includes a 45-unit development in St. Louis and a 175-unit project called The Rockwell in Huntsville, Alabama.
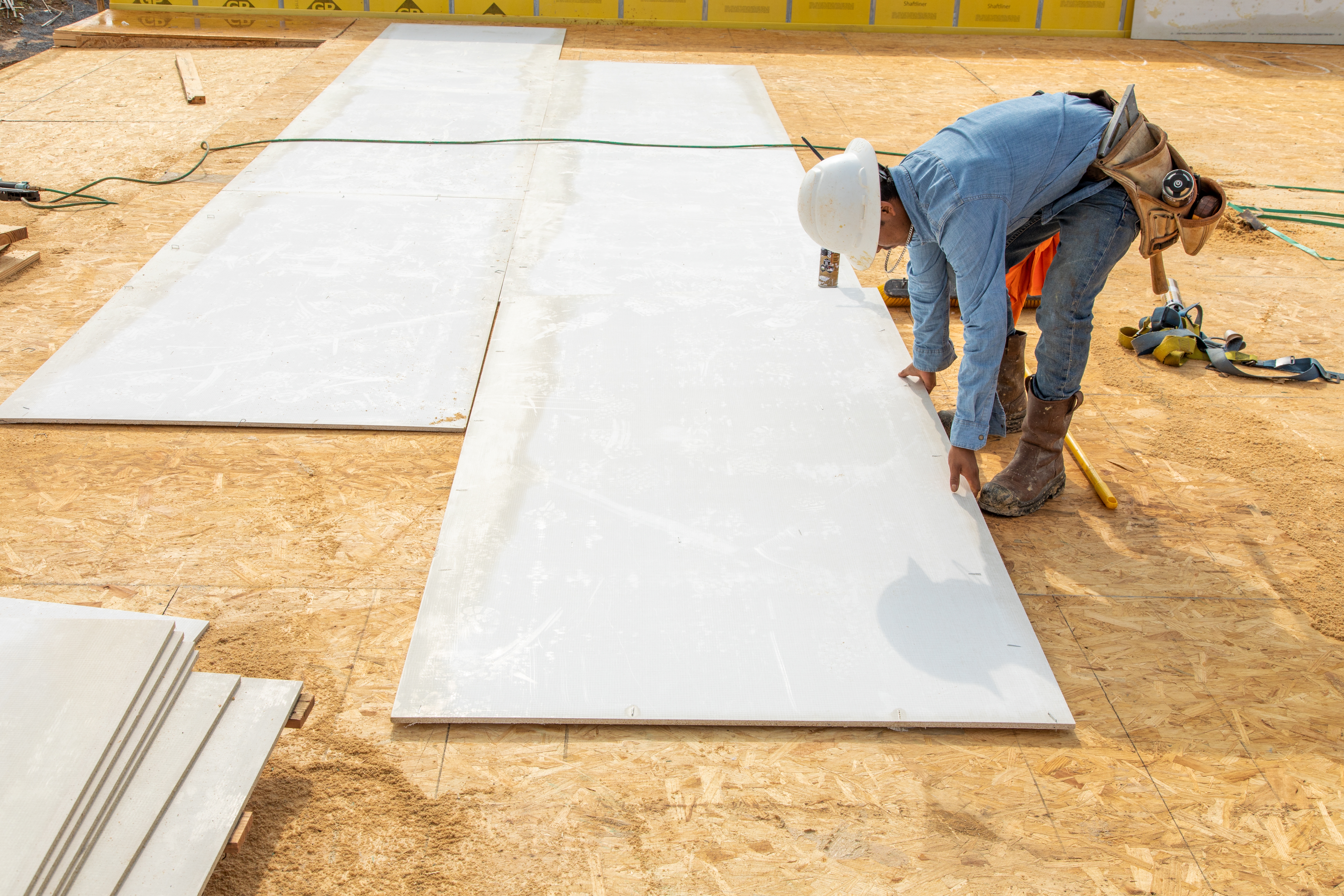
Results and Cost Savings with EXACOR® Products
Now let's talk results.
One major concern in multi-family construction is acoustic performance. Limpert stressed the importance of hitting the right Sound Transmission Class (STC) rating, so they did their own internal sound tests of EXACOR underlayment assemblies—which turned out great.
Installing EXACOR panels was a breeze for their framing crew, which saved them the hassle of hiring specialized contractors for wet-laid gypsum. Avoiding having to hire specialized contractors was also more cost effective for them.
Even though it was their first time using EXACOR, the framing crew quickly got the hang of it. Limpert estimated two to three weeks of savings and around $5,000-7,000 compared to traditional gypsum. These time savings boiled down to simpler cleanup, faster installation, and the elimination of drying times, unlike the relatively clunky wet-laid gypsum process.
Limpert also pointed out the headaches caused by product shortages, such as the national wet-laid gypsum shortage that's plagued many projects.
Considering Arizona's climate, where dryness and winds can be challenging, EXACOR stood out. Limpert highlighted its moisture-free installation, unlike wet-laid gypsum, which can introduce unwanted moisture into the building envelope.
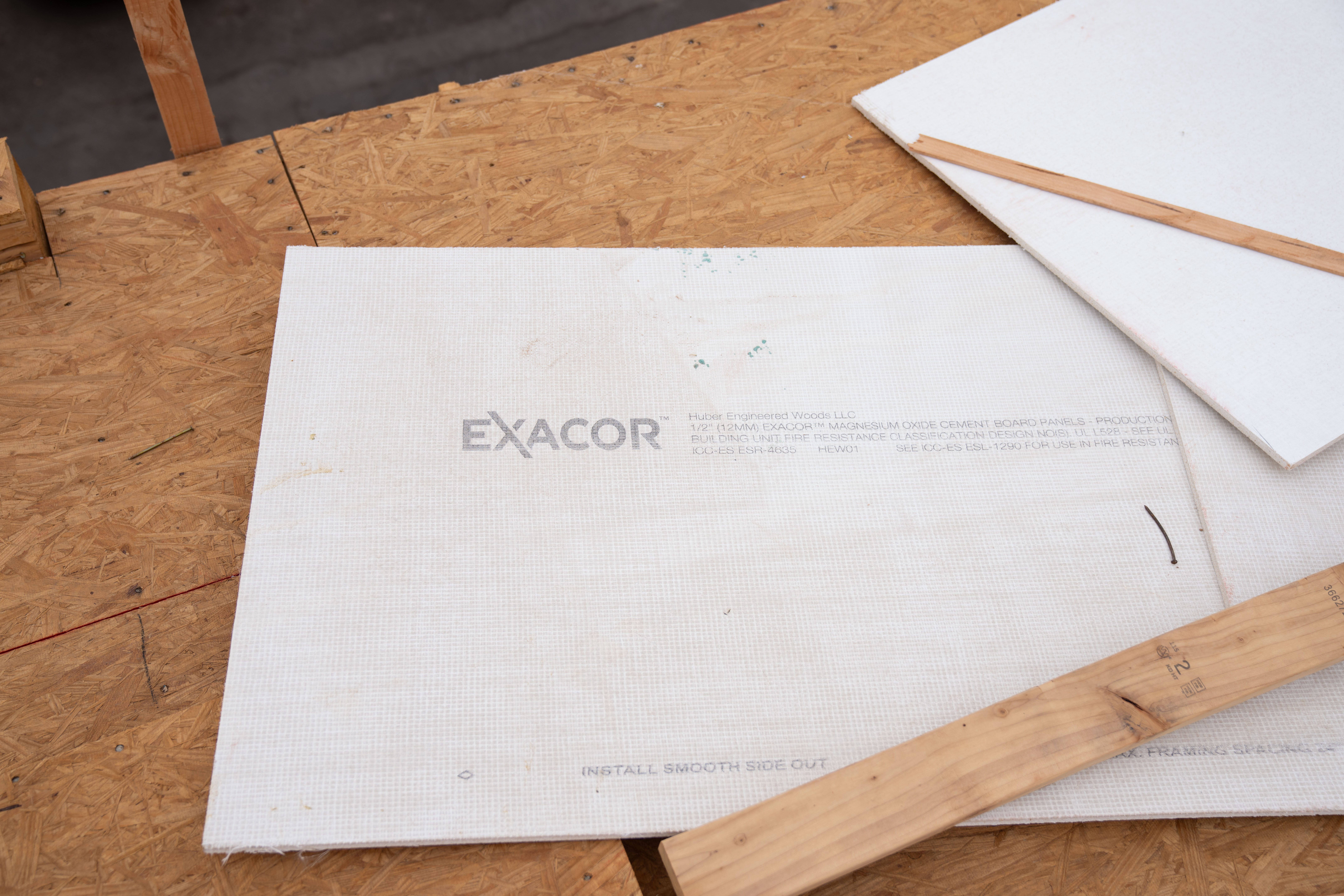
The Future of EXACOR® Products in Construction
Looking ahead, Ridgehouse Construction is all in on EXACOR underlayment in their upcoming Arizona project and are using it for wall applications on other projects. Limpert's been spreading the word about EXACOR's efficiency gains to other interested companies—it's a win-win for smoother construction processes.
As the multifamily construction scene keeps evolving, EXACOR's innovative approach with MgO panels is definitely worth considering.
More questions? Reach out to your local EXACOR expert.